OUR PROCESS
TEARDOWN & QUALIFICATION
Cylinder heads are brought into the tear down department in the condition they were in when they came off the engine.
Step one is to check the cylinder head with a micrometer to see if the cylinder head is thick enough to run through the reman process.
Next step all parts are removed from cylinder head, guides, injector cups, soft plugs (freeze plugs), and all fittings.
Next step is to magnaflux for cracks to see what the next step the cylinder head will go through.


WELDING
The cylinder head is placed on a table made of fire brick.
Fire bricks are placed around the cylinder head to make an oven.
The cylinder head is heated to 1,800 degrees.
Then the welding process starts. This is called fusion welding.
A cast iron rod is used to repair damages. The rod is the same metal that the cylinder head is made of.
Fusion welding is a process that is done when the cylinder head is hot.
After the welding process the cylinder head cools off for approximately ten hours.
Now the cylinder head and the new weld repair will expand and contract together.
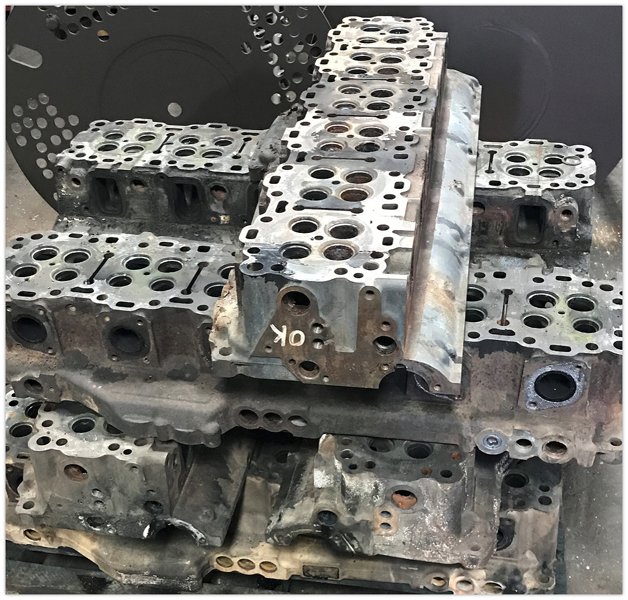

CLEANING
In the cleaning department some cylinder heads need baking to remove all grease and oil.
The cylinder heads that come out of the welding process do not need to be baked.
All cylinder head are run through the wheelabrator.
Then the cylinder head is placed into a tumbler to remove all shot from inside cylinder head.
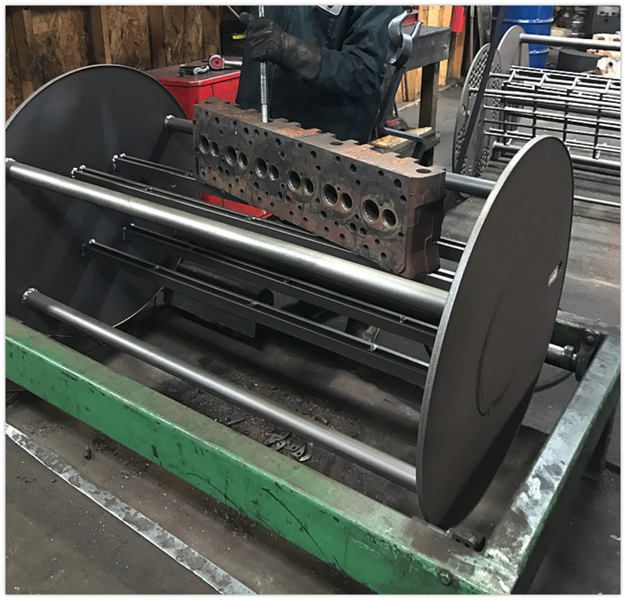
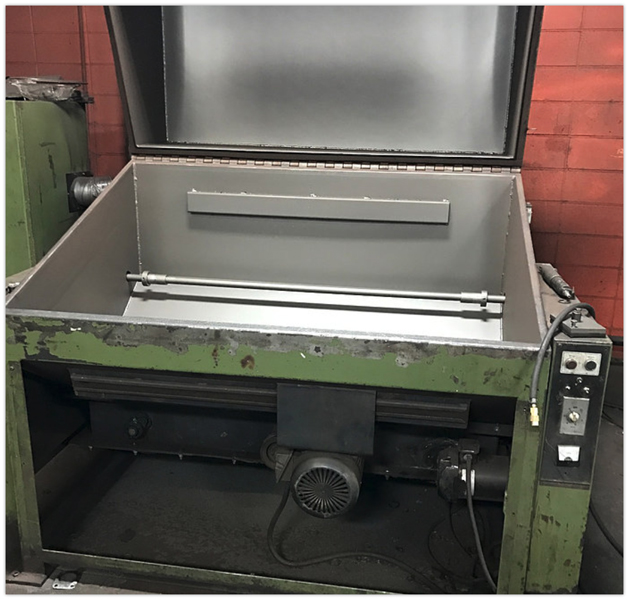
SURFACING
The cylinder head is measured before it goes on the grinder to determine if the cylinder head is in OEM standards.
Most OEM have a maximum that the head can be cut.
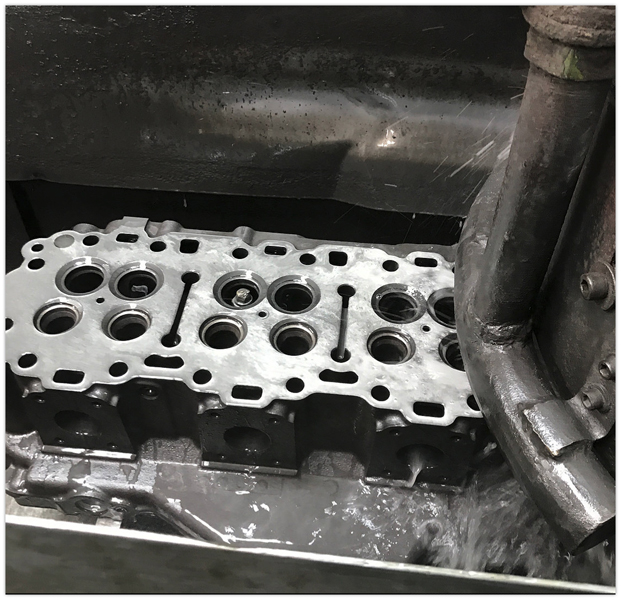
MACHINING
All cylinder heads that are welded need to be machined.
There are many steps in machining. Such as drilling and tapping holes and cutting weld out of injector ports and intake and exhaust ports.
This process is done to get the cylinder head back to OEM standards.

TESTING
All cylinder heads go through the testing process.
The cylinder head is tested to make sure all repairs are correct.
Test plates are bolted to the cylinder head and all holes are sealed off.
Then 80 psi is injected in the cylinder head. then the cylinder head is submerged in hot water.
Cylinder head is then inspected on both sides for leaks.
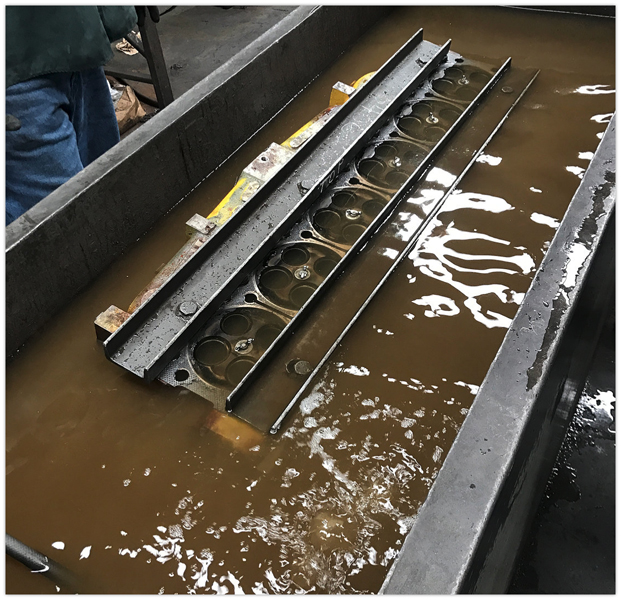

SEAT CUTTING
The cylinder head has been recast the seat nest has be machined out.
The first step is to machine the metal from the seat nest.
Second step is finished with a seat cutter.
Now seats are ready to be installed.
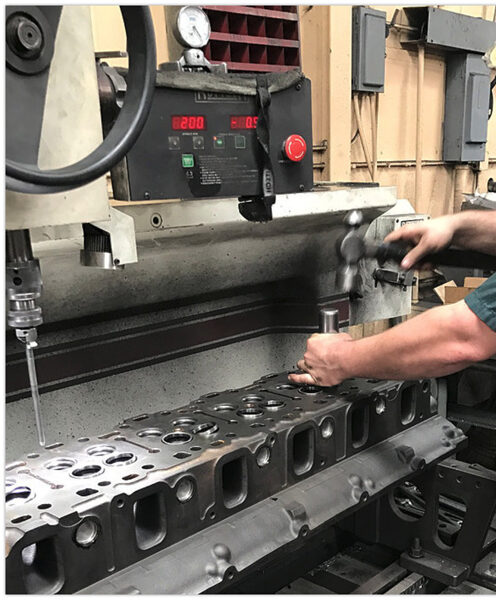
INSPECTION
The inspection station is very important. The inspector has to check every step of the reman process.
Final inspection of the cylinder heads thickness.
Checks the threads in every bolt hole.
Checks the surface of the head.
Checks all sides and back of cylinder head.
Checks all injectors in cylinder head to make sure all injectors are seating properly.
All valve guides are check for protrusion.
All valves are checked for protrusion.
All surfaces are checked.
On over head cam cylinder head camshaft is installed.
Check the over all appearance of cylinder head.
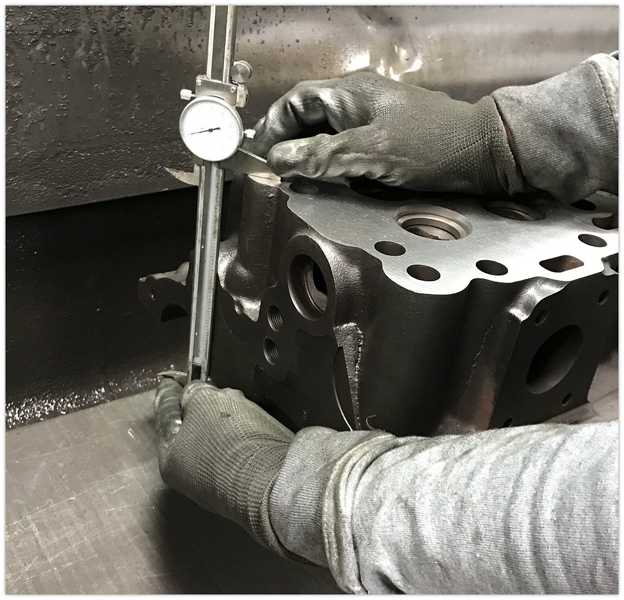
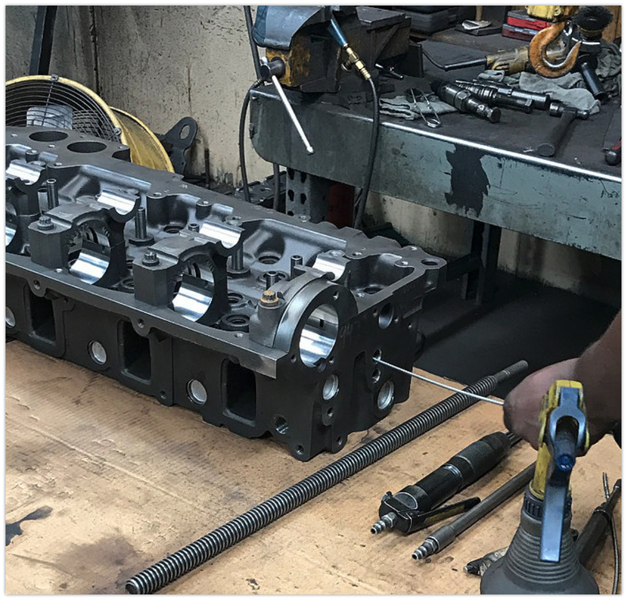
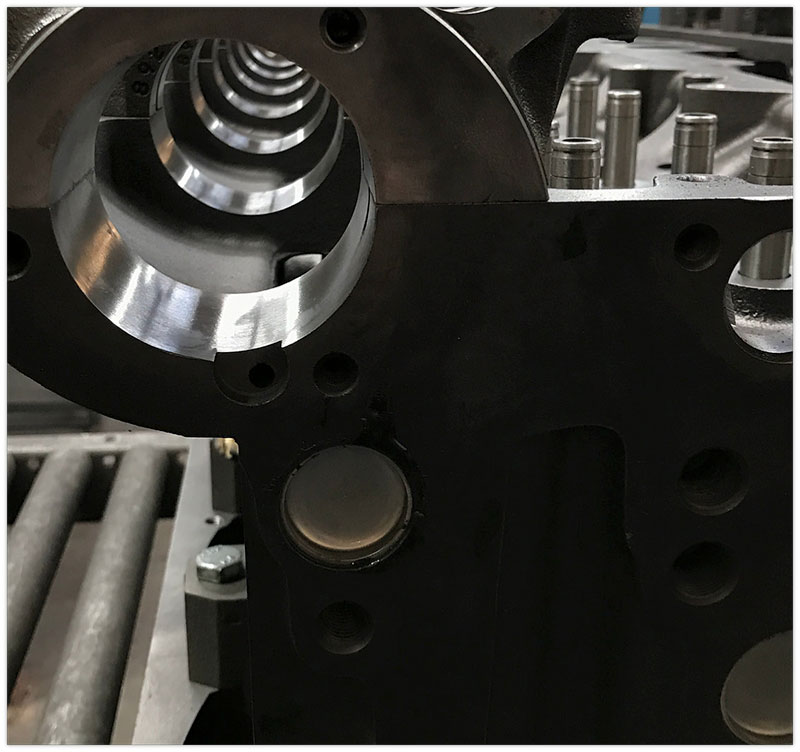
ASSEMBLY
The cylinder head runs through a washer to be cleaned of cutting oil and any kind of debris from the manufacturing process.
The cylinder head has to be identified before assembly.
After going through the wash, valves are installed from the fire deck side of the cylinder head.
Then the cylinder head is laid face down on the assembly line where the air press presses springs and rotocoils down so that keepers can be installed.
The cylinder head is then inspected to make sure all keepers are properly installed.
All valves are vacuumed tested to assure the valves are seating correctly.
After cylinder head is assembled the companies identification number will be stamped onto the cylinder head.
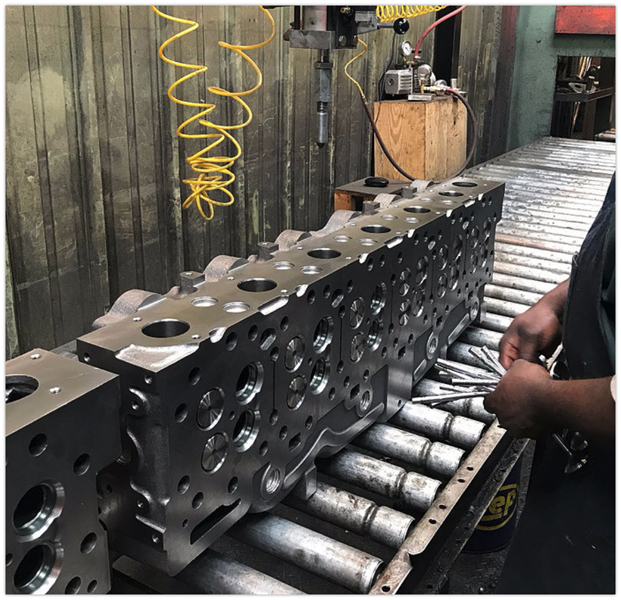
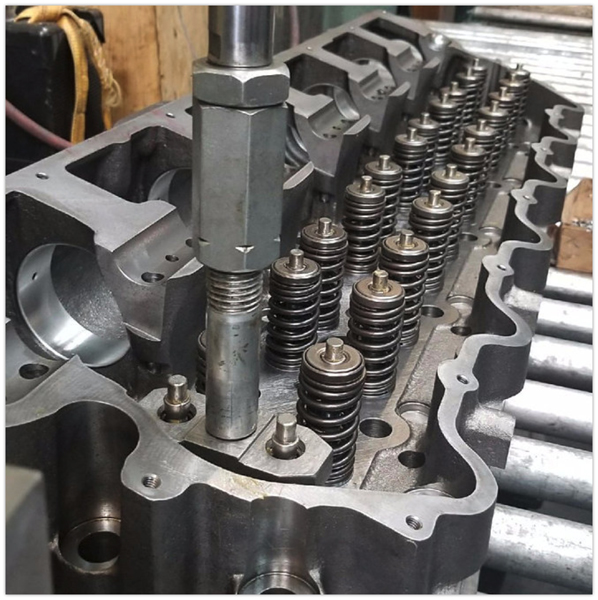
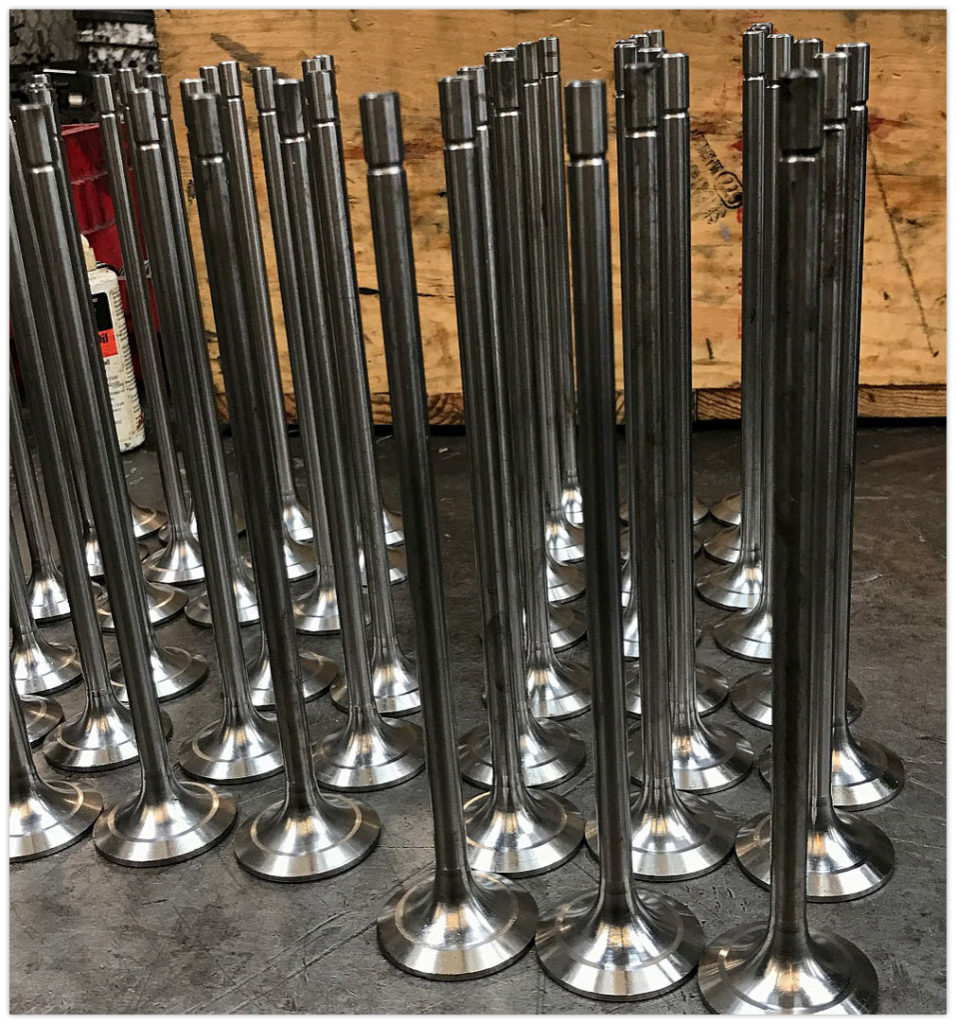
BOXING & SHIPPING
In the shipping department the cylinder head is sprayed with rust preventive solution and a special wax moister barrier paper is placed in the box.
SW Diesel Power, Inc. makes a custom box for every reman cylinder head.
The SW identification number, type of cylinder head, and part number are printed on each box.
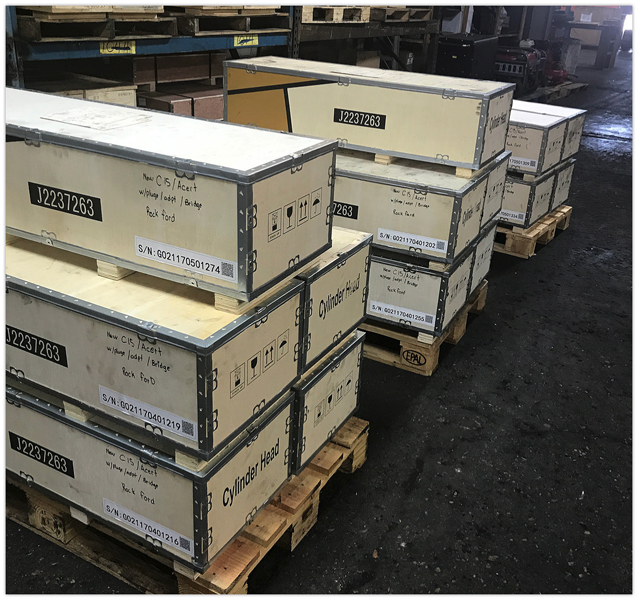